Aircraft engine manufacturers use Abrasive Flow Machining (AFM) to improve airfoil surface finishes on compressor and turbine section blades and vanes. AFM is the preferred process to smooth airfoils on integrated components such as impellers, blisks, and IBR’s when blades have been machined by profile milling or Electrolytic Machining (ECM). Investment cast nozzle segments and stator rings are also efficiently polished. Airfoil and gaspath surfaces are typically improved from as rough as 120 μinch Ra finish to 16 μinch Ra finish or better.
The broached dovetail slots on compressor disks and the firtree slots on turbine disks are simultaneously radiused on both sides using AFM. Complex geometries such as locking ring grooves are also deburred and radiused.
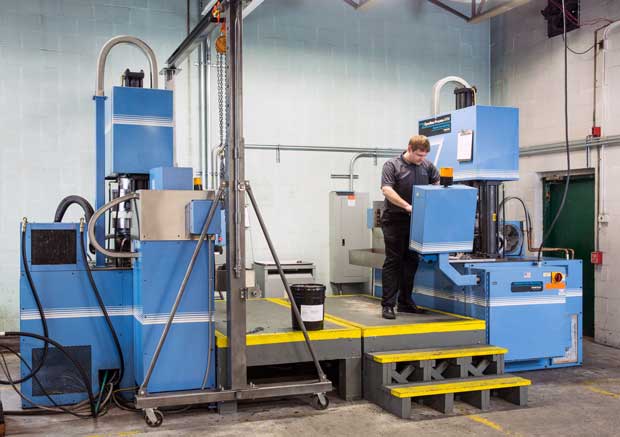
AFM also is used to achieve edge finishes at air cooling holes and oil holes on rotating components such as disks, shafts and seals. The surface finish through the hole is improved and both white layers from abusive machining and recast layers from EDM are removed.